Current design:
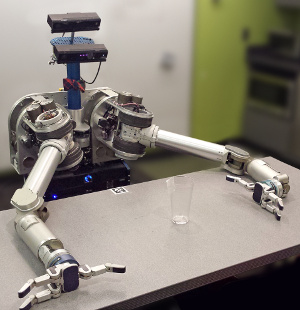
Kinect v2 sensors on a custom pan-tilt.
The neck is a custom 2-DOF pan-tilt neck mechanism. The actuators are the same motors and controllers as used in the Barrett WAM arms. The control software for the 14 joints in the robot’s arms was easily extended to support two extra joints. The neck is force controlled for safe operation around humans. However this sub-system is wearing out and has developed some issues.
The robot’s head is a universal bolt plate for attaching various different sensors, depending on the research application (see Fig. 4 below). Currently HERB has dual Microsoft Kinect v2 sensors (Fig. 1). One depth sensor is used to detect faces and body posture, using the Microsoft SDK. The second identical sensor is used for new perception algorithms developed on Linux and ROS.
An analysis of the robot’s functionality is shown in Table 1 below. Also, as part of the upgrade, some other sub-systems may also be affected. Currently localization of the mobile base is performed using a Hagisonic StarGazer system that detects fiducial markers on the ceiling. The Segway base has its own battery module. A second battery is used to power the on-board computers and a 48 VDC bus for the arm and neck motors.
Advantage | Disadvantage | ||
Base | Segway RMP-200 | ● Self-contained battery. ● Large, pneumatic wheels to drive over obstacles. |
● Differential-drive means that maneuvering in tight spaces requires motion planning using rotation or parallel-parking motions. |
Neck | Custom pan-tilt (uses same motors and controllers as WAM arm) |
● Force controlled actuators reduce risk of pinching human fingers in the joints. | ● Custom one-off design, difficult to modify controller parameters. ● Sensor head falls down when power is turned-off. ● Have to “home” joint encoders when power is turned-on. |
Head | Various sensors including 2D camera, 3D depth sensors (RealSense, Kinect) |
● During research it is typical to change sensors. | ● Poor calibration of sensors (to other sensors or gripper). |
Requirements:
The upgraded robot HERB v3.0 should meet the following requirements:
- A mobile base with mecanum wheels.
So the robot can maneuver in tight spaces around the home and move laterally (side-to-side) in front of a kitchen counter or table. This reduces the need to do whole-body manipulation planning incorporating the base position. - A neck (pan-tilt unit) that holds its position when power is turned-off.
Ideally the actuator should be compliant or backdrivable, for safe human-robot interaction. - A head with 2D and 3D perception sensors.
Ideally a LiDAR sensor for indoor localization and collision detection.
Mobile Base:
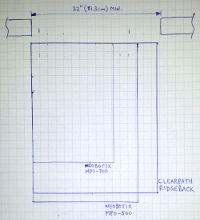
The robot is generally operated indoors on an industrial carpet floor. The majority of research projects have the robot located in front of a table or kitchen counter, so the base needs to drive sideways (laterally). The base should also be narrower than 32 inches so that it can maneuver through an ADA-compliant doorway (Fig. 2), like what is typically found in the home or office.
Various off-the-shelf mobile robot bases were compared, see Table 2 below. The most suitable options were two products manufactured by Neobotix. The team had a predilection for choosing a Mecanum base because it would be easier to write code for a holonomic base and ultimately the Neobotix MPO-500 was selected.
Features | Advantage | Disadvantage | |
Neobotix MPO-500 |
● Mecanum (omni-directional) wheels ● 24 VDC ● Payload: 50 kg (110 lbs) |
● Fits through an ADA-compliant doorway. ● Holonomic motion. ● Very fast and maneuverable (with light payload). |
● Wider base, less clearance with doorway. ● Mecanum wheels use a lot of battery power. ● Shakes (vibration) & noise during driving. ● Difficult to model wheel-slip, for localization. ● Wheels chew-up carpet floor. |
Neobotix MPO-700 Used by existing robots: Similar to: |
● Steerable caster wheels ● 48 VDC ● Payload: 400 kg (882 lbs) |
● Fits through an ADA-compliant doorway. | ● Need to pre-rotate angle of wheels (Small time delay, custom base planner software). ● Width of base is similar to robot’s torso, risk of topple over. ● More expensive than MPO-500. |
Clearpath Ridgeback Used by existing robots: |
● Mecanum (omni-directional) wheels ● 24 VDC ● Payload: 100 kg (220 lbs) ● Lead-time: 10-12 weeks |
● Too wide to fit through doorway. | |
Robotnik Summit XL HL |
● Mecanum (omni-directional) wheels ● 48 VDC ● Payload: 65 kg (143 lbs) |
● High-clearance portal axles increases risk of topple over. ● The top mounting surface is not flat. |
|
MobileRobots aka Adept / Omron Seekur |
● Steerable caster wheels ● Payload: 70 KG |
● Most expensive option. ● Slower to adjust wheel angle than Neobotix. |
|
Segway RMP Omni |
● Mecanum (omni-directional) wheels | ● Mechanical design not suitable. |
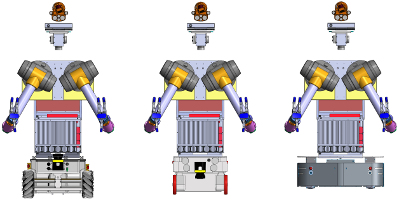
Neobotix MPO-500, Neobotix MPO-700 and Clearpath Ridgeback.
Neck:
Unfortunately there were no robot “neck” modules available off-the-shelf that met all the requirements for a collaborative home robot. We considered building our own pan-tilt mechanism but this was not our expertise.
The Directed Perception (FLIR) PTU D48 has an aesthetically pleasing appearance, however the unit does not always report back the current joint angles after changing position. This is not acceptable for a robot. Therefore we selected the Schunk PW-70. This meets the minimum requirement to support the sensor payload and not come crashing down when power is disconnected.
Features | Advantage | Disadvantage | |
Directed Perception aka FLIR PTU D46 Price: USD$2700 Used by existing robots: |
● 12 – 30 VDC ● Payload: 9 lbs ● Interface: Ethernet, RS-232 |
● Adjustable position-holding using thumb screws. | ● Not strong enough to support MultiSense SL (tested by Clearpath Robotics). ● Must be re-homed when power is turned-on. ● Unit does not always report current position after sending a move command. |
Directed Perception PTU D48 Price: USD$5200 Used by existing robots: |
● 12 – 30 VDC ● Payload: 10 lbs ● Interface: Ethernet, RS-232 |
● Holds position when power is turned-off. ● Signal pass through using slip-rings (not sure if supports GigE ethernet). |
● Must be re-homed when power is turned-on. ● Unit does not always report current position after sending a move command. ● The tilt joint is a pinch-point risk to human fingers. |
Schunk PW-70 Price: USD$8500 Used by existing robots: |
● Height: 165 mm ● 24 VDC ● Interface: RS-232, CAN |
● Holds position when power is removed. | ● Must be re-homed when power is turned-on. ● The tilt joint is a pinch-point risk to human fingers. |
Schunk PW-90 Used by existing robots: |
● Height: 186 mm ● 24 VDC ● Interface: RS-232, CAN |
● Holds position when power is removed. | ● Must be re-homed when power is turned-on. ● The tilt joint is a pinch-point risk to human fingers. |
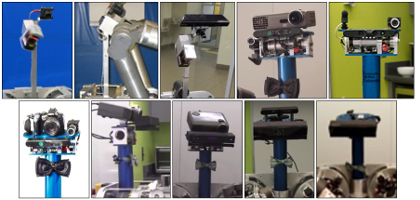
The HERB robot has used various “heads” (sensors) over the years, including a camera, spinning Hokuyo LiDAR, Kinect, Xtion, RealSense and an image projector (Fig. 4). This is typical for a research robot, where project requirements change and 3D sensor technology continues to improve. Ideally the head would also incorporate a microphone array but this was out of scope for the proposed upgrade.
Previously the LiDAR was used to scan objects and create 3D mesh models. This capability has been replaced by the Kinect sensor. However a LiDAR sensor would enable markerless, laser-based localization using features detected in the PointCloud (replacing the StarGazer system). It could also be used for collision detection with a wide FOV (Field of View), to detect humans standing next to the robot, or behind it (Fig. 5-6).
Various perception sensors and combinations thereof were compared (see Table 4 below). The only sensor package available off-the-shelf that met the requirements was the CRL MultiSense SL. This would be combined with an interchangeable RGB-D sensor like the Microsoft Kinect v2 or Intel RealSense. The stereo camera data (from the MultiSense) could be processed by one computer and the depth sensor data by a second computer.
Features | Advantage | Disadvantage | |
Two Kinect v2 + spinning Hokuyo LiDAR |
● 2D camera ● 2 x 3D depth image + point cloud ● 3D laser point cloud |
● Two sensors can be processed by two separate computers. | ● Need to fabricate our own LiDAR rotating mechanism. |
Kinect v2 + Carnegie Robotics MultiSense SL Photos: Price: USD$25000 Used by existing robots: |
● 2D camera ● 3D depth image + point cloud ● 3D stereo depth image + point cloud ● 3D laser point cloud |
● Multiple sensor modalities available together, can be calibrated once. | ● Spinning sensor is a pinch-point risk to human fingers. ● Significantly more expensive than consumer depth sensor. ● The LED spotlights are extraneous. |
![]() with dual Kinect sensors. |
![]() |
Conclusion:
The Schunk PW-70 pan-tilt works well for the “neck”, with stiff and rigid motion control. The “head” is an aluminum bracket that integrates a CRL MultiSense SL, Microsoft Kinect v2 and Intel RealSense sensors. This combination provides flexibility for different projects.
The final upgraded robot HERB v3.0 is shown in Fig. 11. Future work is to develop improved software for localization and base motion planning.
![]() with arms removed. |
![]() |
![]() upgraded HERB v3.0 |
This work was conducted with members of the Personal Robotics Lab at CMU.
References: |
[1] S. S. Srinivasa, D. Berenson, M. Cakmak, A. Collet, M. R. Dogar, A. D. Dragan, R. A. Knepper, T. Niemueller, K. Strabala, M. V. Weghe and J. Ziegler,
“HERB 2.0: Lessons Learned From Developing a Mobile Manipulator for the Home,” in Proceedings of the IEEE, Vol. 100, No. 8, August 2012. |
[2] R. Brooks, L. Aryananda, A. Edsinger, P. Fitzpatrick, C. Kemp, U-M O’Reilly, E. Torres-Jara, P. Varshavskaya and J. Weber, “Sensing and Manipulating Built-for-Human Environments”, International Journal of Humanoid Robotics (IJHR), March 2004.
|
[3] E. Klingbeil, A. Saxena and A. Y. Ng, “Learning to Open New Doors”, in Proceedings of Robotics Science and Systems (RSS) workshop on Robot Manipulation, June 2008.
|